The most important aspect of the integrated hydraulic system hydraulic valve block design is that the hydraulic circuit block must be in accordance with the hydraulic system schematic.
The most important aspect of the integrated hydraulic system hydraulic valve block design is that the hydraulic circuit block must be in accordance with the hydraulic system schematic. The specific principles are as follows:
1. Before designing the hydraulic valve block, first determine which part of the oil circuit can be integrated.
2, the number of components included in each valve block should be moderate, too many components of the valve block is large, difficult to design and process; too few components, the integration is not significant, resulting in material waste.
3. In the design of hydraulic valve block, the oil path should be as simple as possible, and the deep hole, inclined hole and process hole should be reduced as much as possible.
4. The hole diameter of the hydraulic valve block should match the flow rate. In particular, it should be noted that the through hole must ensure sufficient flow area. Pay attention to the direction and position of the inlet and outlet ports. It should match the overall arrangement of the hydraulic system and the pipe connection form. And considering the manufacturability of the installation operation, components with vertical or horizontal installation requirements must be guaranteed to meet the requirements after installation.
5. For hydraulic components that must be adjusted during work, the convenience of operation and observation should be considered during design.
1 Adjustable hydraulic components such as relief valve and speed control valve should be placed in the position where the adjustment handle is easy to operate.
a. Overflow valve: In order to protect the motor from starting or stopping the pump, it is completed in the low pressure zone. Therefore, the electromagnetic spill valve is selected, and the working demand of high pressure and large flow is guaranteed, and the overflow valve with the insert is selected;
b. Reversing valve: Its function is to ensure that the hydraulic shearing cylinder has a smooth commutation, no impact, and it is guaranteed to work only when it needs to be cut, so as to avoid malfunction;
c. Balance valve: The function of the valve is to realize the differential control of the translation control, and the cylinder is differentially used for the fixed cutting of the hydraulic shearing, and the valve acts when the billet is sheared;
d. Unloading valve: In order to ensure the quick return of the hydraulic shear, a normally closed valve is added at the bypass, and the valve only works when the hydraulic shear returns;
e. Cartridge valve: The cartridge valve is selected as the differential control.
2 Components and key components such as proportional valves and servo valves that should be frequently inspected should be above or outside the valve block for easy assembly and disassembly.
3 A sufficient number of pressure measuring points should be set in the design of the hydraulic valve block for the valve block to be debugged.
4 For hydraulic valve blocks with a weight of 30kg or more, lifting screw holes should be provided.
5 Under the premise of meeting the requirements of use, the volume of the valve block should be as small as possible.
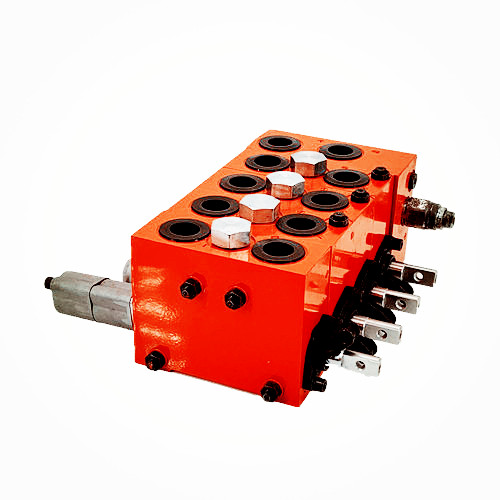
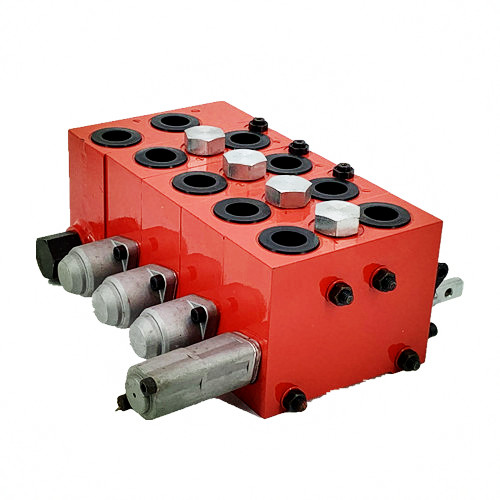